Le TAKT TIME Le terme « takt time » ( Taktzeit) est d’origine Allemande, ce terme désigne initialement le tempo dans un morceau de musique. Employé dans le milieu industriel, il correspond à la durée idéale de production calée sur la demande client. Comment calculer le takt time ? Le takt time T T se définit par la formule suivante : Takt time = Temps disponible/nombre d'unités voulues Exemples : Un îlot de production travaillant en 3 équipes, chaque équipe travaille 7 heures, la demande moyenne mensuelle est de 25200 pièces. - 20 jours ouvrés - Temps quotidien disponible : 1260 minutes - Demande moyenne quotidienne : 1260 pièces Takt time = 1260/1260 = 1 minute par produit Comment utiliser le takt time ? Dans un premier temps on peut comparer les temps de cycle (machine) ou temps de travail (hommes) au takt time par l’intermédiaire d’un graphique en « bâton ». ...
Articles
Les 5S
- Obtenir le lien
- X
- Autres applications

Les 5S Les 5S, c’est quoi? Le 5S est une méthode pour améliorer et maintenir l’organisation des postes de travail • Les 5S représentent 5 disciplines pour maintenir visuellement un lieu de travail • Les 5S sont fondamentaux à l’amélioration continue. La méthode 5S tire son origine de la première lettre de chacune des cinq opérations qui la compose . 5 principes simples. En Japonais En Français S eiri -> S upprimer S eiton -> S ituer S eiso -> S cintiller S eiketsu -> S tandardiser S hitsuke -> S uivre Historique : Taïchi Ohno a créé le concept original “4S”, d’organisation des postes de travail et de contrôles visuels au s...
Les 14 états d'esprit du KAIZEN
- Obtenir le lien
- X
- Autres applications
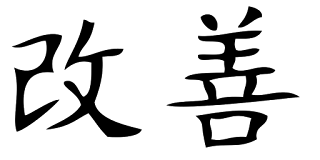
Les 14 états d'esprit du KAIZEN Ne pas juger, ne pas blâmer Abandonner les idées fixes, refuser l’impossibilité de changer la situation Chercher ce que l’on peut faire au lieu d’expliquer ce que l’on peut pas faire Réaliser aussitôt les bonnes propositions d’amélioration Oublier la perfection et obtenir dès maintenant 60% de l’objectif Trouver des idées dans la difficulté et rendre si nécessaire le problème insupportable Corriger immédiatement chaque erreur sur le terrain Trouvez la cause racine en utilisant les 5 pourquoi? et trouver ensuite la solution Faire preuve d’intelligence collective et ne pas attendre l'idée géniale d'une personne Essayer puis valider Mesurer le progrès et communiquer celui-ci Savoir copier et améliorer Le processus conduit au résultat L'amélioration continue est infinie et commence chez soi N'hésitez pas à consulter notre site internet www.optiprocessconseil.fr et à nous contacter pour toute question ...
SMED
- Obtenir le lien
- X
- Autres applications
Le SMED Origine du SMED : Le SMED est un outil développé par Shiego Shingo en plusieurs étapes. En 1950 : Alors employé à l'usine Mazda, on lui demande d’analyser la production de 3 presses ne fonctionnant pas à pleine capacité. En 1957 : Alors employé à l'usine Mitsubishi Dans ce cas on lui demanda d’améliorer la productivité d’une grande rectifieuse (une machine-outil industrielle). Le dernier pas fut franchi avec une analyse d’un temps de réglage d’une presse chez Toyota. A matériel semblable, les Allemands de WW mettaient 2h alors que cela nécessitait 4h chez Toyota. Pour résumer : Shigeo Shingo mit environ 20 ans pour formaliser le bon sens dans une méthode simple et évidente ! SMED ? S ingle M inute E xchange of D ies SMED est l'abréviation de l'anglais single-minute exchange of die(s) “Changement de matrice en moins de 10 minutes”. Le terme SMED et sa traduction sont très peu importants. Ce qu’il fau...
Les 10 avantages du ONE PIECE FLOW
- Obtenir le lien
- X
- Autres applications
Les 10 avantages du ONE PIECE FLOW Les recherches montrent que le surmenage est l’une des principale source de blessure sur le lieu de travail. Lorsque nous passons au flux pièce à pièce, nous limitons le besoin de soulever des palettes lourdes et des conteneurs de matières. Avantage N° 2 : Détection des défauts Le fait de travailler en ONE PIECE FLOW permet détecter plus rapidement les défauts, et ainsi d’éviter de trier ou de retoucher un lot complet. La mise en place d'actions correctives se fait alors immédiatement après détection du défaut. Avantage N°3 : Améliore la flexibilité Le ONE PIECE FLOW est plus rapide que le traitement par lots. Ce facteur de rapidité nous permet d'attendre plus longtemps pour planifier la commande (et toujours livrer à temps). De plus cela permet d'augmenter la flexibilité lors de changement de dernière minutes (modification de commande client par exemple). Avantage N°4 : Améliore l'évolution des équipements ...
Lean management et les 8 gaspillages
- Obtenir le lien
- X
- Autres applications
Lean Management et les 8 gaspillages Le Lean Management a pour but de mettre à contribution tous les acteurs d'une entreprise afin de supprimer les différents gaspillages qui impactent la performance d'une entreprise, Les gaspillages étant les opérations n'apportant pas de valeur ajoutée pour le client. Le Lean Management s'attaque aux 7 gaspillages (muda) + 1 : Surproduction Surstockage ou Stocks Inutiles Transports et Déplacements Inutiles Opérations ou traitements inutiles Mouvements Inutiles Erreurs, Défauts et rebuts Temps d’Attente et Délais Sous-utilisation des Compétences 1. Surproduction Produire plus que le besoin du client. Produire avant la commande. Réaliser une tâche qui ne répond à aucune demande ni exigence client.Le pire des gaspillage car source d’autres gaspillages Provoque le ralentissement, voire l’arrêt du flux. 2. Surstockage ou Stocks Inutiles Tout ce qui n’est pas indi...